Cutting processes are those in which a piece of sheet metal is separated by applying a great enough force to caused the material to fail. The cut being formed may follow an open path to separate a portion of material or a closed path to cutout and remove that material. The geometric possibilities for a cutting process depend on the technology used, but most are capable of cutting out any 2D shape. Some of the most common sheet metal cutting processes use shearing forces to separate the material. A description of those processes can be found in the previous section. In this section, cutting processes that use other forces, such thermal energy or abrasion, will be discussed. Some common methods of sheet metal cutting that use such forces include the following:
Laser cutting
Laser cutting uses a high powered laser to cut through sheet metal. A series of mirrors and lenses direct and focus a high-energy beam of light onto the surface of the sheet where it is to be cut. When the beam strikes the surface, the energy of the beam melts and vaporizes the metal underneath. Any remaining molten metal or vapor is blown away from the cut by a stream of gas. The position of the laser beam relative to the sheet is precisely controlled to allow the laser to follow the desired cutting path.
This process is carried out on laser cutting machines that consist of a power supply, laser system, mirrors, focusing lens, nozzle, pressurized gas, and a workpiece table. The laser most commonly used for sheet metal cutting is a CO2 based laser with approximately 1000-2000 watts of power. However, Nd and Nd-YAG lasers are sometimes used for very high power applications. The laser beam is directed by a series of mirrors and through the “cutting head” which contains a lens and nozzle to focus the beam onto the cutting location. The beam diameter at the cutting surface is typically around 0.008 inches. In some machines, the cutting head is able to move in the X-Y plane over the workpiece which is clamped to a stationary table below. In other laser cutting machines, the cutting head remains stationary, while the table moves underneath it. Both systems allow the laser beam to cut out any 2D shape in the workpiece. As mentioned above, pressurized gas is also used in the process to blow away the molten metal and vapor as the cut is formed. This assist gas, typically oxygen or nitrogen, feeds into the cutting head and is blown out the same nozzle as the laser beam.
Laser cutting can be preformed on sheet metals that are both ferrous and non-ferrous. Materials with low reflectivity and conductivity allow the laser beam to be most effective – carbon steel, stainless steel, and titanium are most common. Metals that reflect light and conduct heat, such as aluminum and copper alloys, can still be cut but require a higher power laser. Laser cutting can also be used beyond sheet metal applications, to cut plastics, ceramics, stone, wood, etc.
As previously mentioned, laser cutting can be used to cut nearly any 2D shape. However, the most common use is cutting an external profile or complex features. Simple internal features, such as holes or slots are usually punched out using other sheet metal processes. But highly complex shapes and outer part boundaries are well suited for laser cutting. The fact that laser cutting does not require any physical contact with the material offers many benefits to the quality of the cuts. First, minimal burrs are formed, creating a smooth edge that may not require any finishing. Secondly, no tool contact means only minimal distortion of the sheet will occur. Also, only a small amount of heat distortion is present in the narrow zone affected by the laser beam. Lastly, no contaminates will be embedded into the material during cutting. Although not a quality issue, it is worth noting that the lack of physical tool wear will reduce costs and make laser cutting cost effective for low volume production.

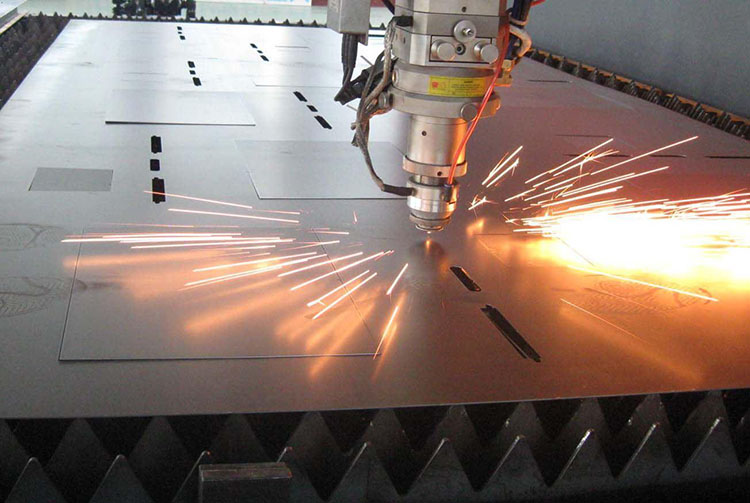
Capabilities
- Sheet thickness: 0.02-0.50 in.
- Cutting speed: 30-500 IPM (1000 IPM feasible)
- Kerf width: 0.006-0.016 in. (0.004 in. feasible)
- Tolerance: ±0.005 in. (±0.001 in. feasible)
- Surface finish: 125-250 μin
Design rules
- Edges – Burrs are minimal, but can be further reduced by using a thinner sheet stock.
- Corners – Rounded corners are preferred to sharp corners. Interior corners must have a minimum radius equal to the laser beam radius.
- Holes – Minimum hole diameter should be approximately 20% of sheet thickness, down to 0.010 inches. Laser-cut holes will have a slight natural taper.
- Multiple sheets can be cut at once to reduce cost
Plasma cutting
Plasma cutting uses a focused stream of ionized gas, or plasma, to cut through sheet metal. The plasma flows at extremely high temperatures and high velocity and is directed toward the cutting location by a nozzle. When the plasma contacts the surface below, the metal melts into a molten state. The molten metal is then blown away from the cut by the flow of ionized gas from the nozzle. The position of the plasma stream relative to the sheet is precisely controlled to follow the desired cutting path.
Plasma cutting is performed with a plasma torch that may be hand held or, more commonly, computer controlled. CNC (computer numerically controlled) plasma cutting machines enable complex and precision cuts to made. In either type of plasma torch, the flow of plasma is created by first blowing an inert gas at high speed though a nozzle pointed at the cutting surface. An electrical arc, formed through the flow of gas, ionizes the gas into plasma. The nozzle then focuses the flow of plasma onto the cut location. As with laser cutting, this process does not require any physical tooling which reduces initial costs and allows for cost effective low volume production.
The capabilities of plasma cutting vary slightly from laser cutting. While both processes are able to cut nearly any 2D shape out of sheet metal, plasma cutting cannot achieve the same level of precision and finish. Edges may be rough, especially with thicker sheets, and the surface of the material will have an oxide layer that can be removed with secondary processes. However, plasma cutting is capable of cutting through far thicker sheets than laser cutting and is often used for workpieces beyond sheet metal.
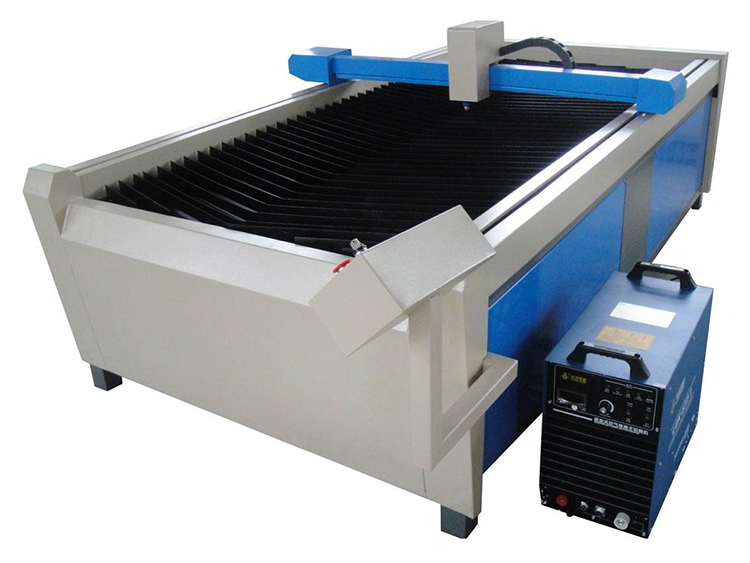
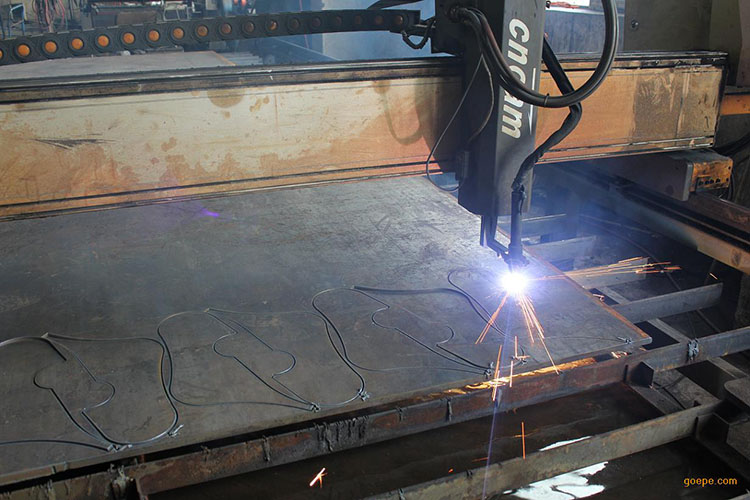
Water jet cutting
Water jet cutting uses a high velocity stream of water to cut through sheet metal. The water typically contains abrasive particles to wear the material and travels in a narrow jet at high speeds, around 2000 ft/sec. As a result, the water jet applies very high pressure (around 60,000 psi) to the material at the cut location and quickly erodes the material. The position of the water jet is typically computer controlled to follow the desired cutting path.
Water jet cutting can be used to cut nearly any 2D shape out of sheet metal. The width of the cuts is typically between 0.002 and 0.06 inches and the edges are of good quality. Because no burrs are formed, secondary finishing is usually not required. Also, by not using heat to melt the material, like laser and plasma cutting, heat distortion is not a concern.
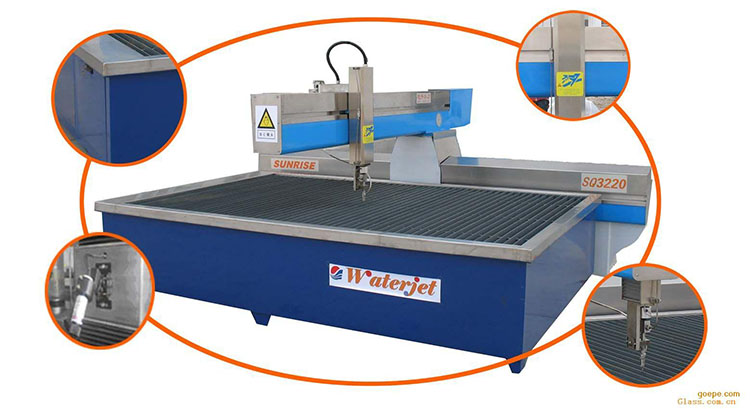
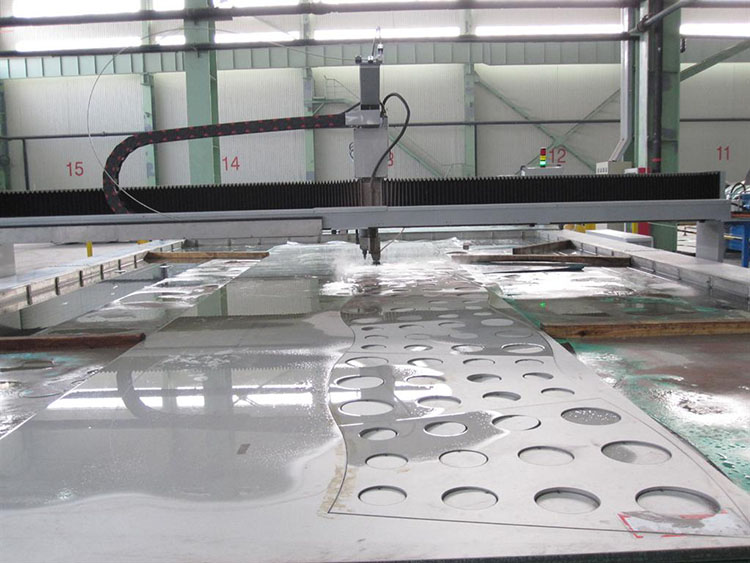
近期评论